Tiny House Trailer Bolts: Welding Went Well
Calling All Local Welders
“Yea, how much would it cost to weld threaded rod to a trailer for a tiny house? Like sixteen pieces.” Tiny house enthusiasm ensues. Confusing welding terms are shared. Various prices are quoted.
Tenacity for Learning or Stubborn Frugality
The price sounded like it would cost around $250. As a growing DIY guy, I’m more and more reluctant to hire help. I’d rather learn the skill–and overcome my reservations and fears about trying it. Welding the rod to the trailer was a prime example of this tenacity for learning (the nice spin on the behavior). The decision was finalized after talking with two friends who have welded before. They confirmed my pa’s MIG welder should do the trick–or at least I should try it and see how strong the welds would be.
Enter the MIG Welding Unit
Pa purchased a 90 Amp Flux Wire Welder by Chicago Electric from Harbor Freight for $115 awhile back. It states that it’s not suited for aluminum or stainless steel. I forget what threaded rod we used–but I hope it wasn’t stainless now! They have a stronger unit that does stainless steel for $199. These units don’t require gas–they eject heated-up metal as they make their arc, which is when you use electricity to heat metal to bond the two metals. Like all welders–these puppies need to be grounded and emit dangerous levels of electricity–all precautions should be taken.
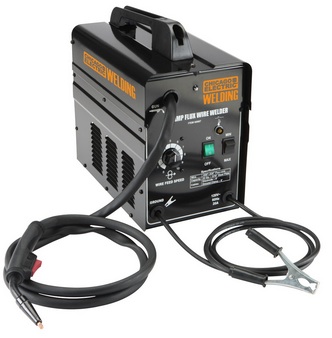
Welding Preparations
You shouldn’t weld over paint–nasty smelling and it will compromise the welds, so after grinding down my beautiful paint job, I marked lines on each side of the threaded rod after making sure the rods were straight up and down and level. I also precut all of the rods. As stated before, I had 6 inches of steel tube framing and 6 1/2 inches of subfloor with the sill plate. I added another two inches for a buffer and to have enough for the Simpson Strong Tie HTT5 to fit over. I rounded up and went with 15 inch pieces, so I would need 20 ft of threaded rod ($60-70 depending on grade and type). *I cut off around 2-3 inches in the end, so I had too much.

Tools:
- Welder
- Welding Gloves
- Welding Mask (Automatic preferred) *Check batteries in it!
- 10 Gauge Extension Cord. We used a 12 Gauge Extension Cord.
- Stronger Welder Might Need 30+ Amp Plug. Our 20-amp did the deed.
- Cheap Steel Brushes
- Extra Welding Wire Spool. We used two spools.
- Slag Chipping Hammer
Materials:
- Cut Pieces of Threaded Rod
Advice from Ollie
One of my friends with welding experience gave me the following tips and expectations and also led me through a welding practice session at his workshop:
-
With the MIG welder, you’ll be using Flux Core Wire. This is messy. Will create slag (black glassy layer stuff) which you’ll have to chip off or scrub with a wire brush. Use non-flammable clothing because this stuff with spray you a bit. *Followed advice and got sprayed quite a bit. I didn’t need hammer to chip off slag; the steel brushes were enough.
-
Your welder has lower amperage, so you won’t be able to fine tune its setting as well as other welders. You’ll probably need it on max. Adjust the wire feed to get a nice bacon sizzle that doesn’t shoot off too much slag. *Yes, it was on max, and the wire feed was around 8. This was high because we had a large gap to fill in.
-
Make sure to have a strong extension cord. *Got one.
-
I looked at your welder’s manual. It has 220% duty cycles, so after every 2 minutes of welding, you’ll have to let the welder cool for 8 minutes at its max power setting. *We rested it for about 5 minutes. Pa wasn’t patient.
-
You can use zinc primer for the welded area. *Didn’t use. But after cleaning the welds, I did quickly use rust converter as a primer (otherwise surface rust would occur overnight).
-
Use a mask for zinc vapor, or you’ll get metal fever. *Yikes–I wore my respirator; never got a crazy fever.
- Take a sledge hammer and hit the rod after. If it holds, you should be fine. *We did this—hit the rod multiple times to really test it. They were holding very well! Yay! Also, I had to sledge some of the rods a bit when putting the 3/4 inch plywood over them.
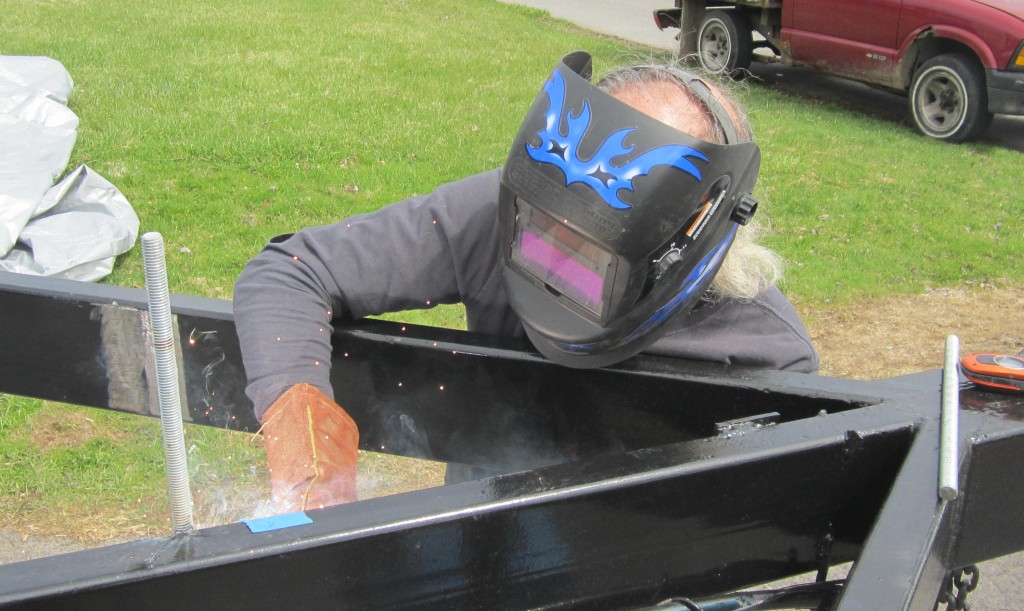
Threaded Rod Placement
I didn’t have to weld along the height of the whole steel tubing (6 inches), but I thought it was a nice overkill idea. My friend Ollie explained that the more space in-between the metals, the more you can inject metal into that in-between area, bonding the metals while creating a stronger weld. For this reason, I chose to run the welds along the entire tubing instead of a butt weld (just placing the rod on top of the trailer framing–little surface area between the metals ). I heard butt welds can be sometimes finicky and unreliable, too….probably depends on the welder. For me, I was going for maximum strength; however, placing the rod along the tubing shifted the holes in my sill plate–they wouldn’t be in the center of the plate anymore, but it would still work out, so “I made my bed to lie in.” One alternative option would be to drill a hole in the frame. Place rod into the hole–weld around the top of it. You also could add an additional hole and welding point through the bottom of frame.
Ugly but Strong Welds
Pa started off welding the first side of the trailer. He owned the welder and had a little experience. He’d weld a small bead at the top and bottom while I held the rod in place. Then, he’d start filling in the entire length (my overkill request). His initial welds were pretty ugly tumors; sorry Pa. This was because we didn’t have a high enough setting on the wire feed for the large gaps we had to fill in. Also, Pa didn’t really get the welding gun in close enough for that nice consistent bacon sizzle. We’ll place the blame on his glasses. Regardless of looks, we banged on them with a lot of force with the sledge hammer–they weren’t budging or going anywhere! Success!
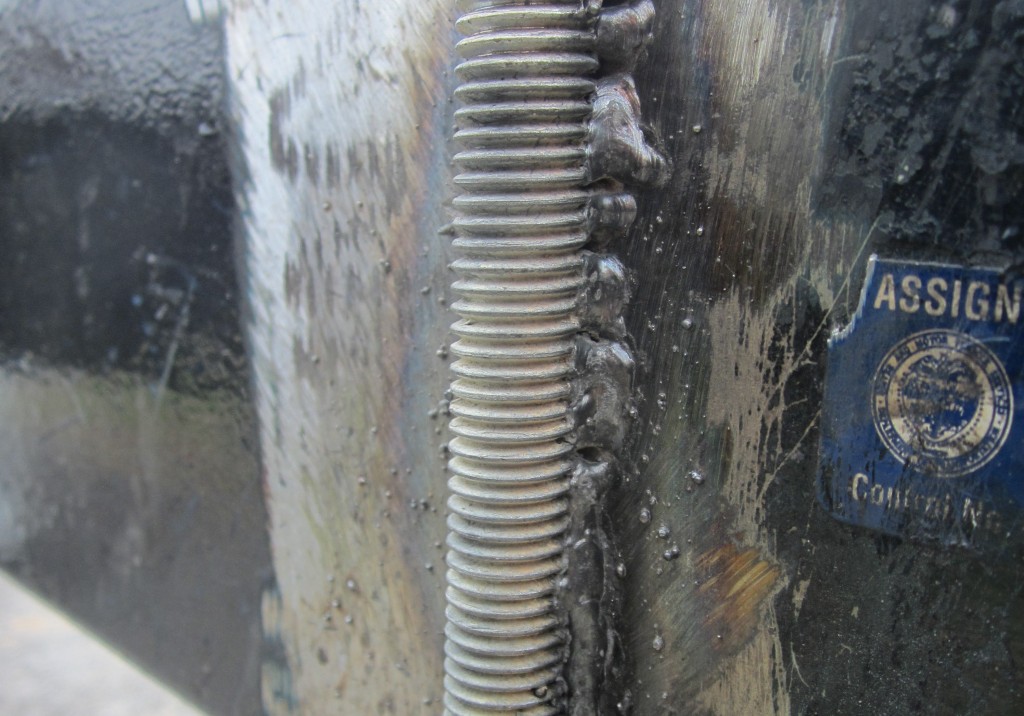
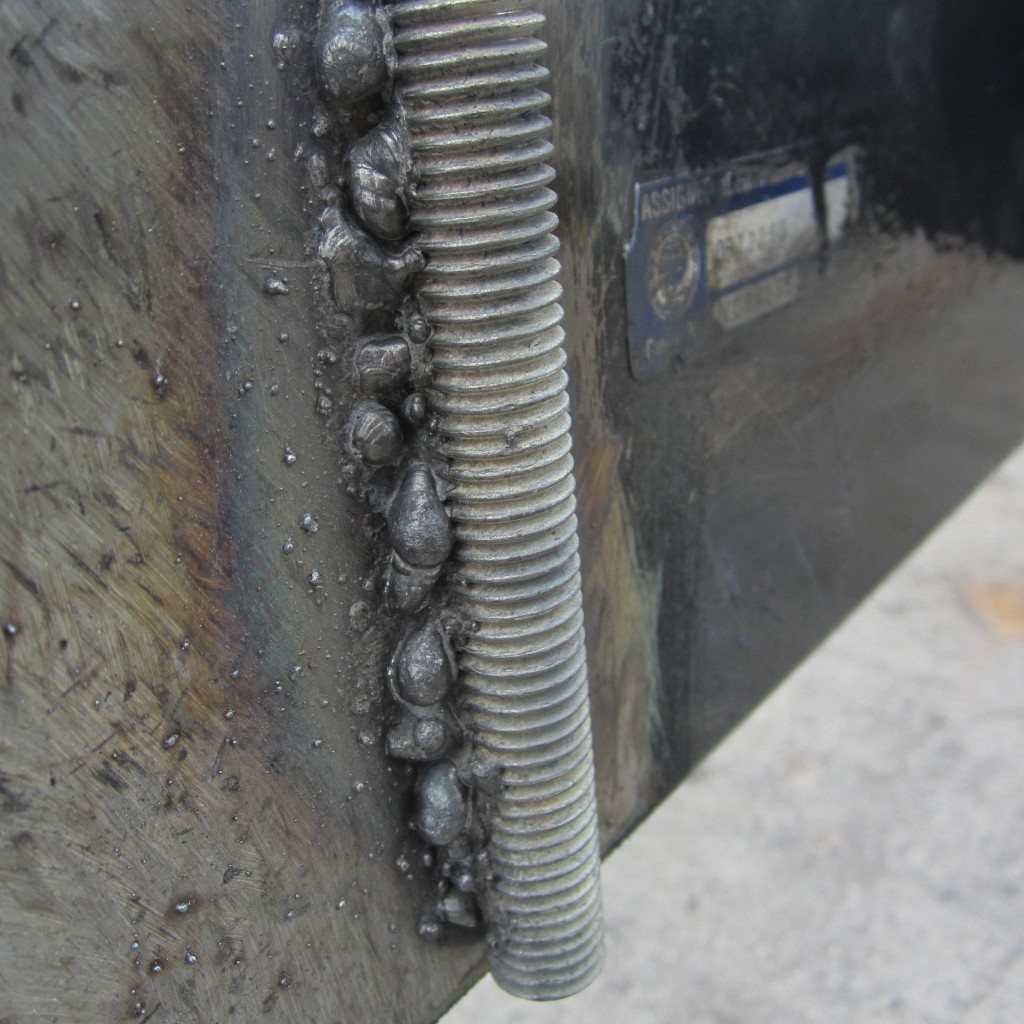
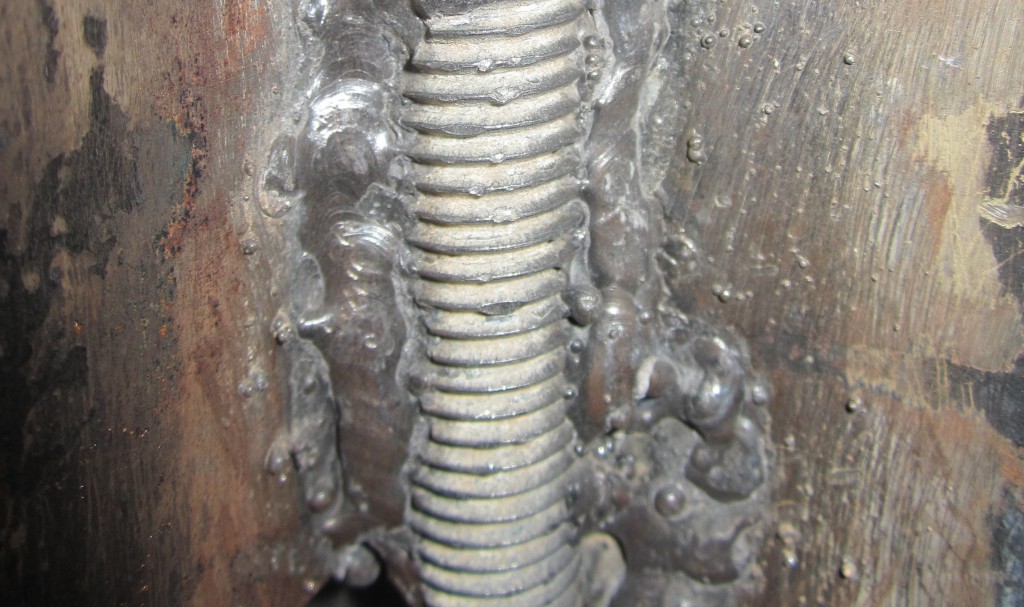
Round 2: Just Me and the MIG
We didn’t finish all of the welds on day one because it started to rain. On day two, it was just me. Before I got started, I noticed that surface rust already started to form on the bare metal areas. I should have applied a metal primer or the rust converter as a primer ASAP yesterday. Lesson learned.
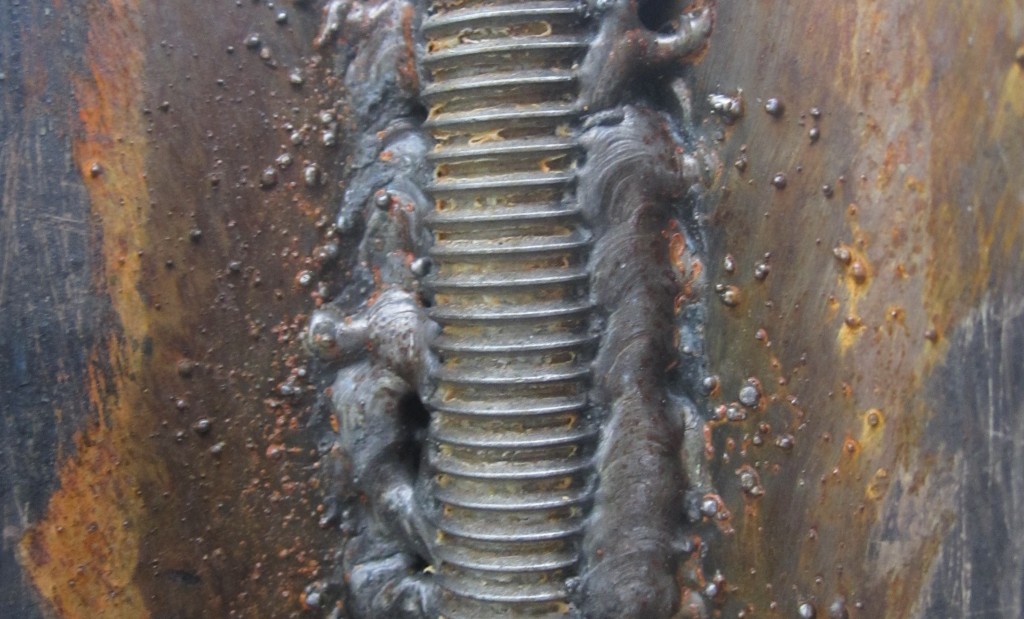
After cleaning off the rust and putting on the rust converter, my welding debut commenced. I read through the welder’s manual, and I made sure I followed all of the safety steps. Definitely make sure to ground the welder with the clamp. We would use the previous bare metal bolt to do this (a painted surface could weaken the ground connection). I held the rod myself and got some beads on it. I found that if I got the needle closer and slowly weaved left to right, I could get some less ugly welds. I felt a little giddy during the process! I didn’t have to hire a welder and picked up a new skill. I hope to weld some furniture legs in the future (you can always grind down those ugly welds!). Don’t forget to prime and paint the new bolts! Here were some of my less ugly welds:
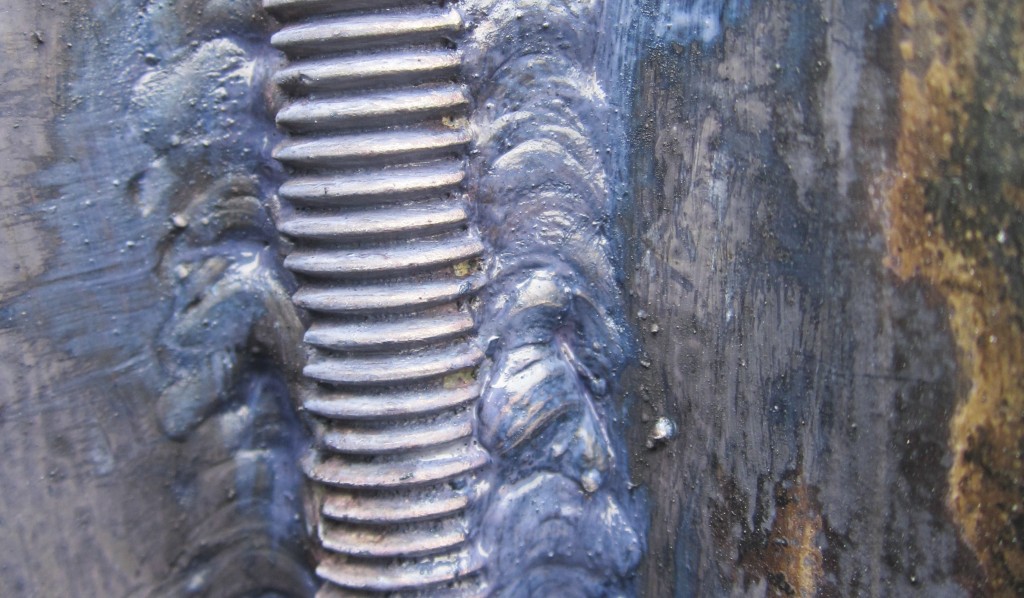
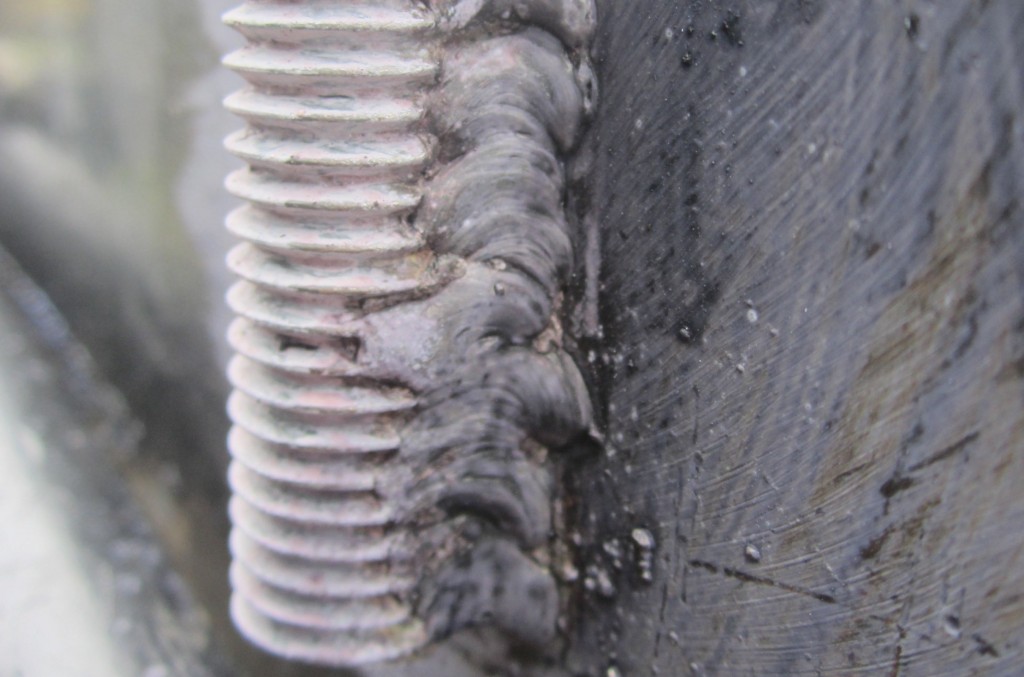
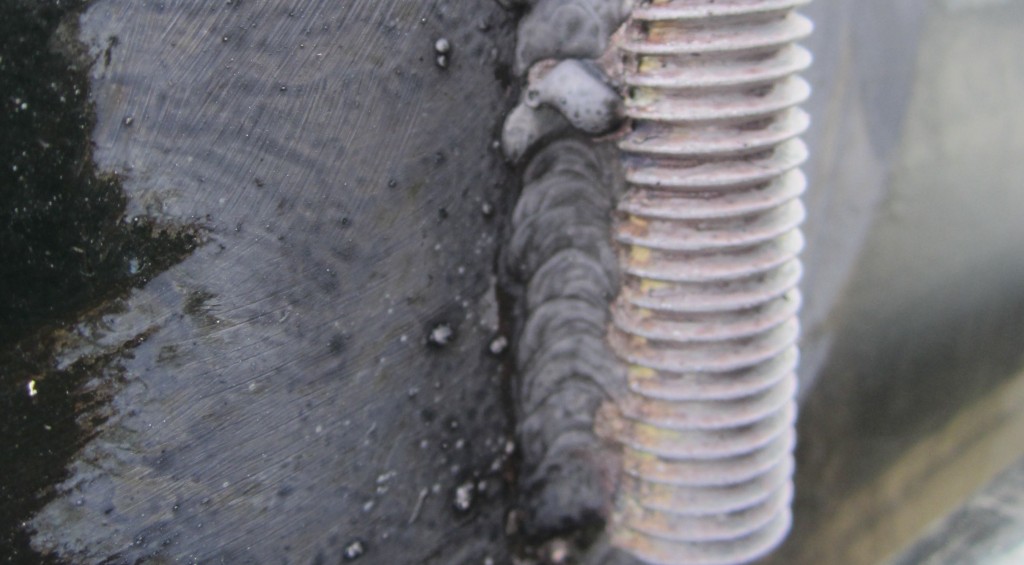
The reins are ours,
Chris
Reflections, Hindsight, and Alterations:
- It’s really helpful to reach out and see if you have any friends who can weld.
- If you don’t want to invest in the welder or can’t find one to borrow, cut the threaded rod with an angle grinder with a metal cut-off blade. Having the rods prepared will cut down the cost of having a welder come over.
- After placing the steel hold-downs over the rods, I ran into some issues. Because the rod wasn’t in the center of my sill plate, some hold-downs would stick out slightly beyond the thickness of the wall. I could either grind down the hold-downs or just carve the back of my pine siding to make it work.
- One rod was in the middle of our door! I put a nut on the bolt and shaved the rest of the rod off. I was able to carve a piece out of the bottom of the door frame to fit it over the nutted bolt, allowing me to utilize that bolt to help me at least hold the subfloor to the trailer at that point.
- Between a lot of welding overkill along the 6″ steel tubing and cutting off 2-3 inches at the top– I wasted a lot of threaded rod. Shit. Should have just welded 3-4 inches along the frame and trusted my measurements to and above the sill plate. Don’t forget to add the Simpson Steel Hold-down built-in washer and height of the nut. I’d add an inch of wiggle room beyond that get more.